What is spaghetti architecture?
As the name implies, spaghetti architecture is similar to a spaghetti plate: all tangled. This rends systems expensive to maintain and prone to failure.
In regards to supplier management, spaghetti architecture means several systems in several departments with several processes. This makes it harder for companies to maintain and update supplier data, having negative impacts on finance and performance.
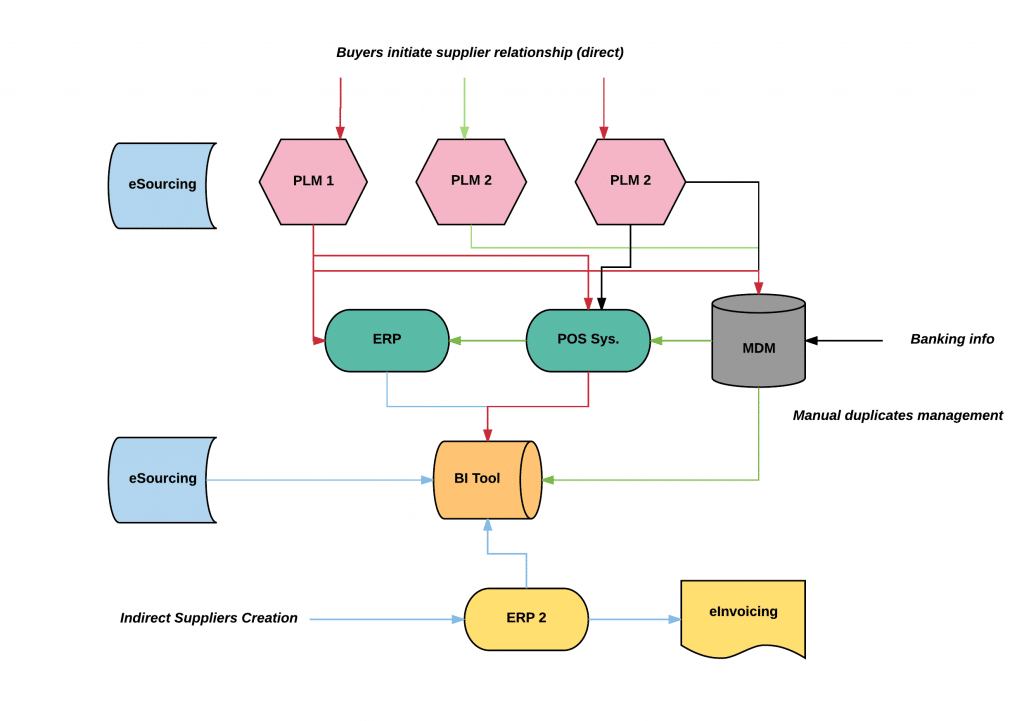
1 – Multiple systems create chaos
Having multiple systems complicates the supplier creation process: many different entry points and various contributors. And it does not only concerns companies with external growth but all companies.
If various users from various departments can access supplier data, each can create and update it without any process or control. Unicity check, in such a context, is quite impossible. This generates duplicates, inaccurate data, and risk.
But it is not always easy to start a “One ERP for all” project. Several factors come into play, whether due to the company history/context or investment capacity. Investing in SIM (Supplier Information Management) middleware will help you bring supplier management back under control.
2 – Team (un)productivity
Fragmented data over multiple systems kill global efficiency. A spaghetti architecture implies a labyrinth synchronization between different software. It sometimes requires buyers and AP clerks to update supplier data in different systems manually.
This duplication of tasks means hours of unproductive work and less focus on strategic added-value tasks. According to AMR Research, employees spend eight times less energy on managing supplier relationships in companies equipped with a SIM.
3 – Maintenance Costs
A complex system architecture means costs – whether for SAAS or On-premise models. IT departments face challenges every day in maintaining the consistency of data flows between all systems. If we only focus on the supplier/buying side, this already means ERPs, BI tools, eSourcing suites, and P2P solutions.
They have to deal with referential synchronization, technical issues and conflicts, data mapping, real-time interfaces, and nightly batches everywhere! However, changing a system configuration requires a deep impact analysis.
Centralizing supplier data in a SIM solution will clarify the architecture and help reduce the number of systems. It can also optimize their usage, thus reducing the costs of the global IT architecture.
Conclusion
As more enterprise processes are being digitized through specific solutions, most IT departments need to manage multiple systems. Whether SaaS or On-Premises, they also have to manage associated integration flows. These complex architectures can generate data corruption.
It is now a priority to streamline the data management process and set up governance. Otherwise, Procurement & Finance departments (and the whole company) will be exposed to risks, fraud, extra costs, and lack of productivity.